Case Studies
How Leading Brands Label with Loftware
Discover how businesses around the world are transforming their labeling operations, overcoming compliance challenges, and driving supply chain efficiency with Loftware’s industry-leading solutions.
Our collection of success stories and case studies highlights real-world results from organizations across industries — from manufacturing and chemicals to life sciences and retail.
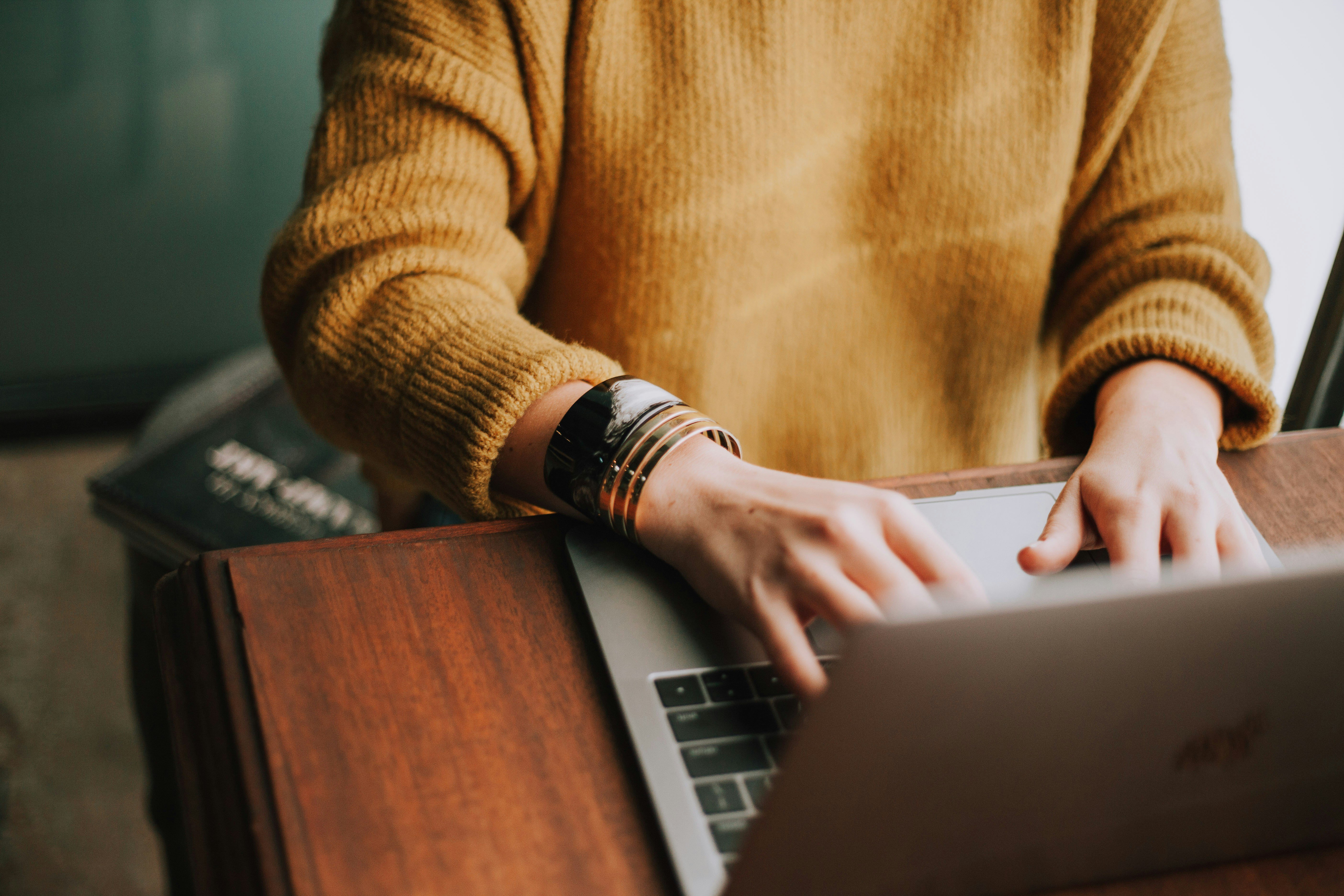
Imagine what Loftware can do for you
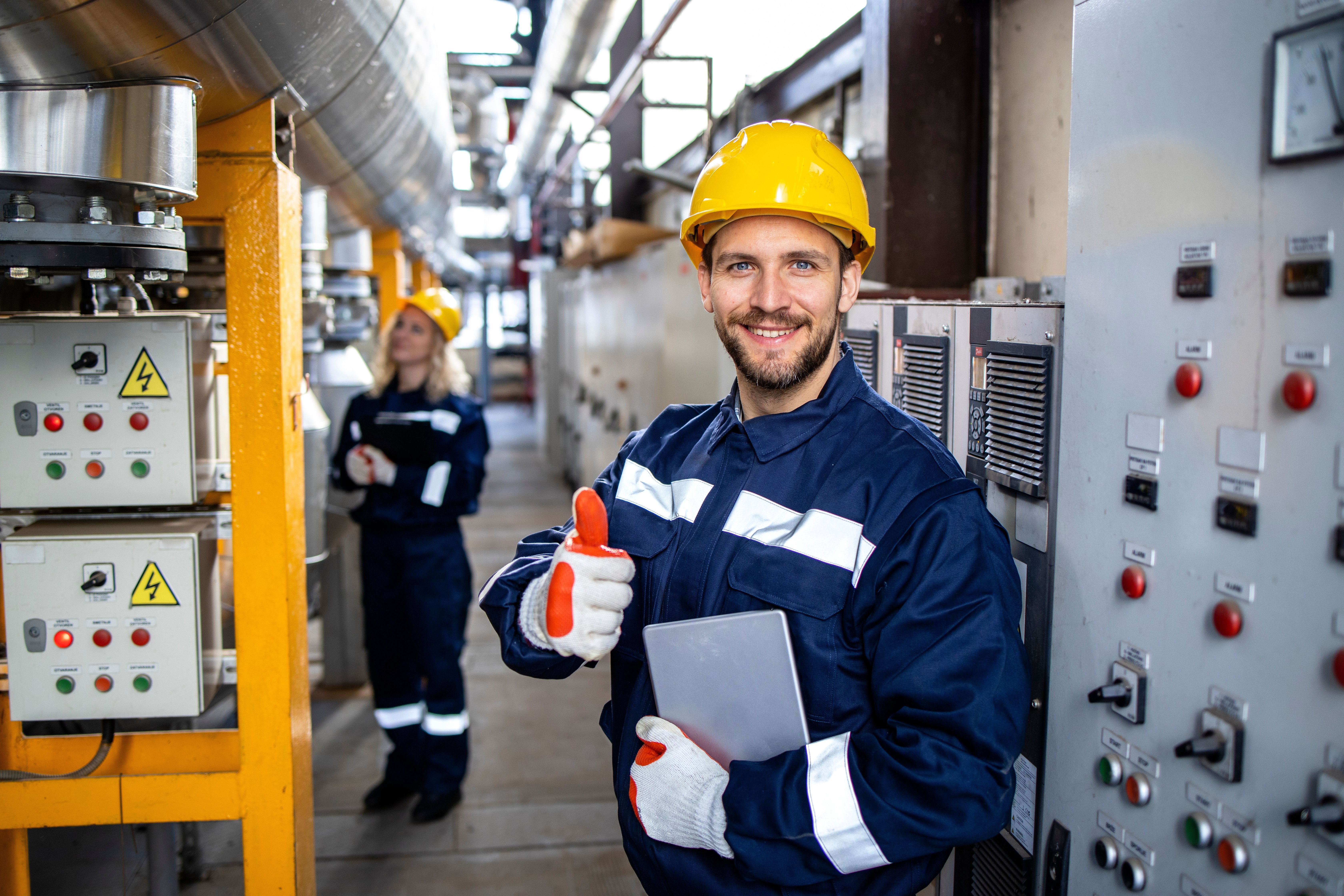
Case Study
Nice North America brings cloud-first strategy to labeling with Loftware Cloud
Read this case study to learn how Nice North America increased operational efficiency and streamlined labeling...
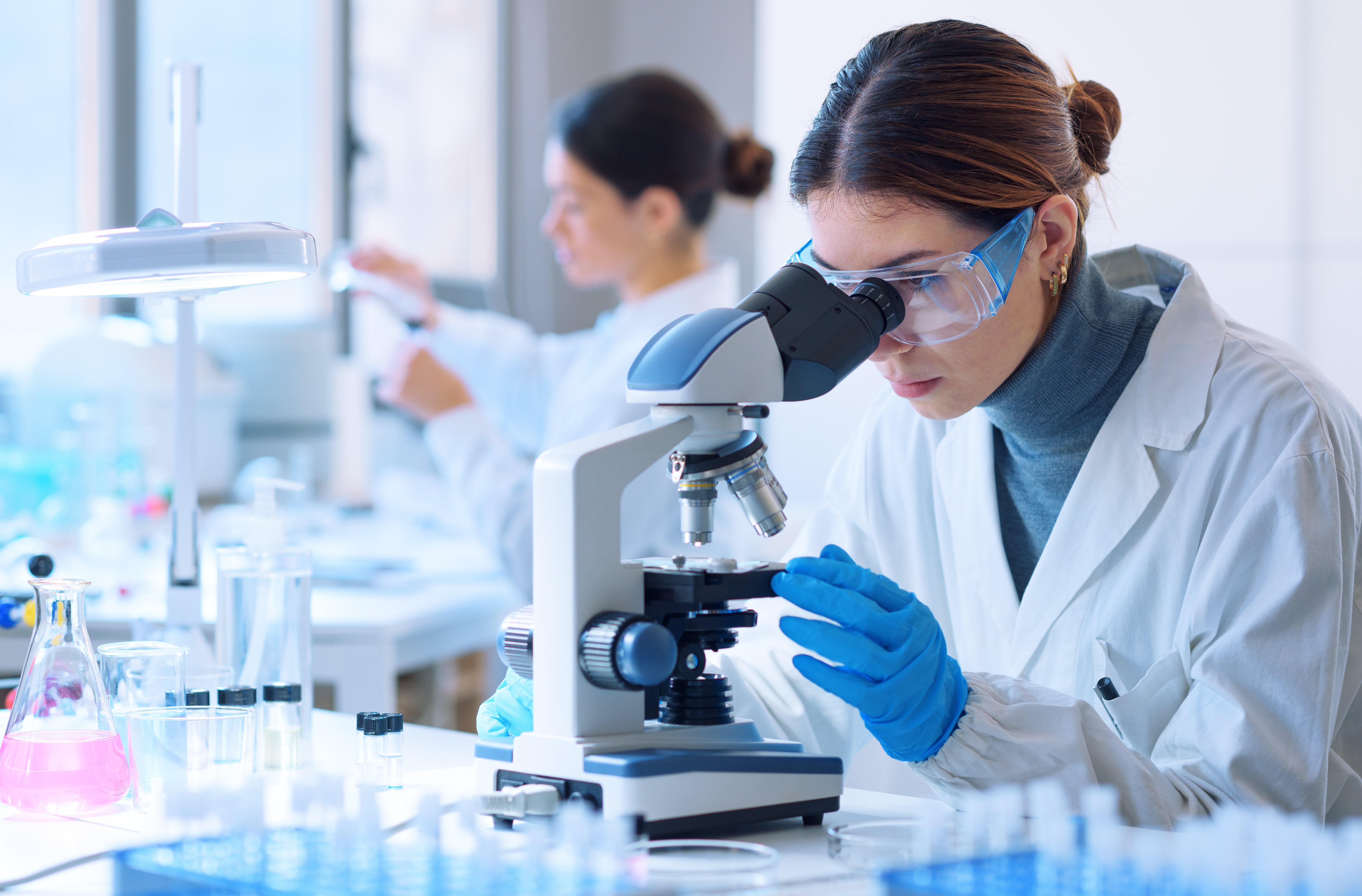
Case Study
Orion Corporation’s artwork management transformed by Loftware Smartflow
Learn how Orion, a global pharmaceutical company, streamlined its packaging operations and supported business growth by...
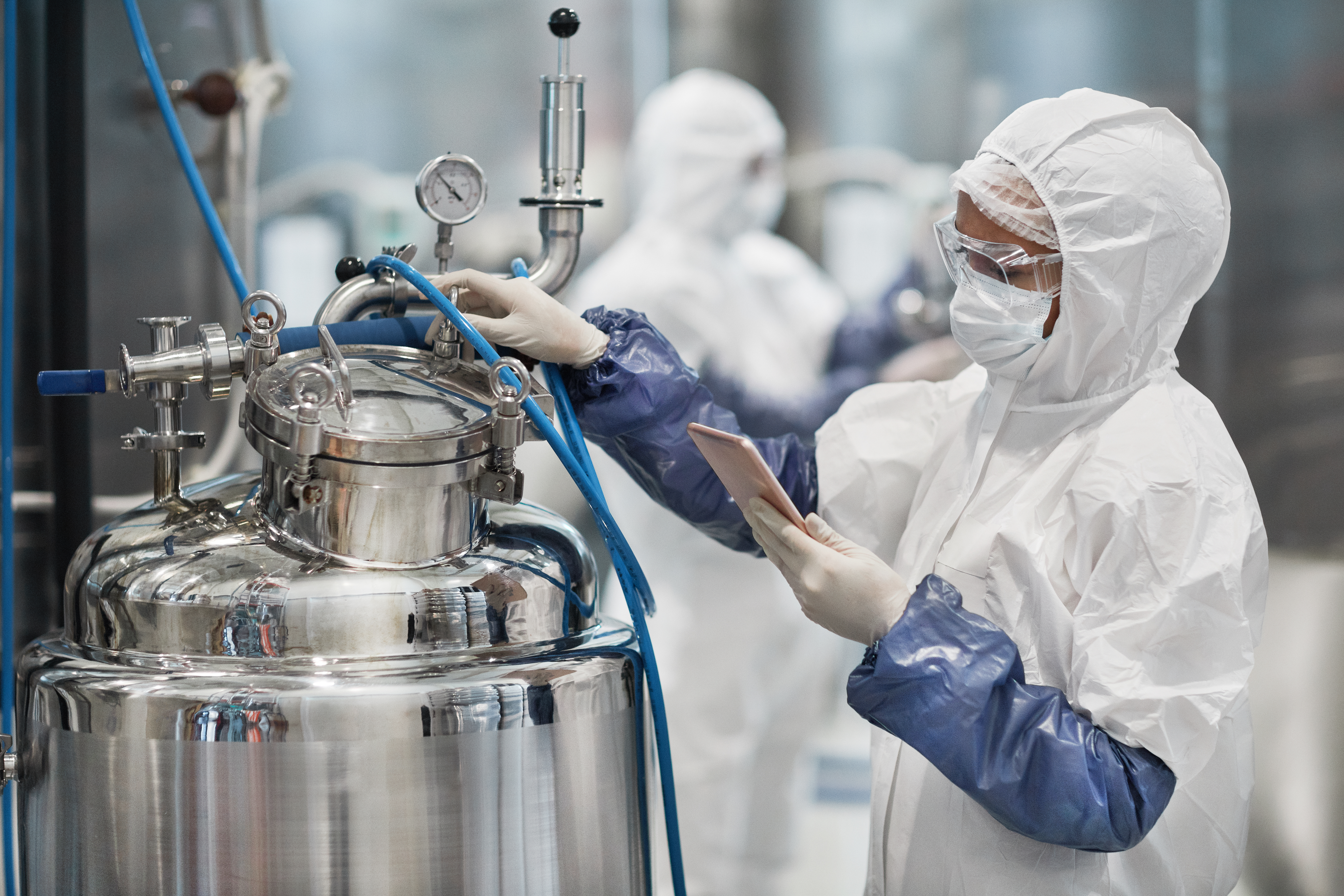
Case Study
How Lubrizol Boosted Compliance, Efficiency, and Sustainability by 30% with Loftware SAP Integration
Discover how Lubrizol achieved cost savings, improved accuracy, and sustainability by integrating Loftware with SAP....
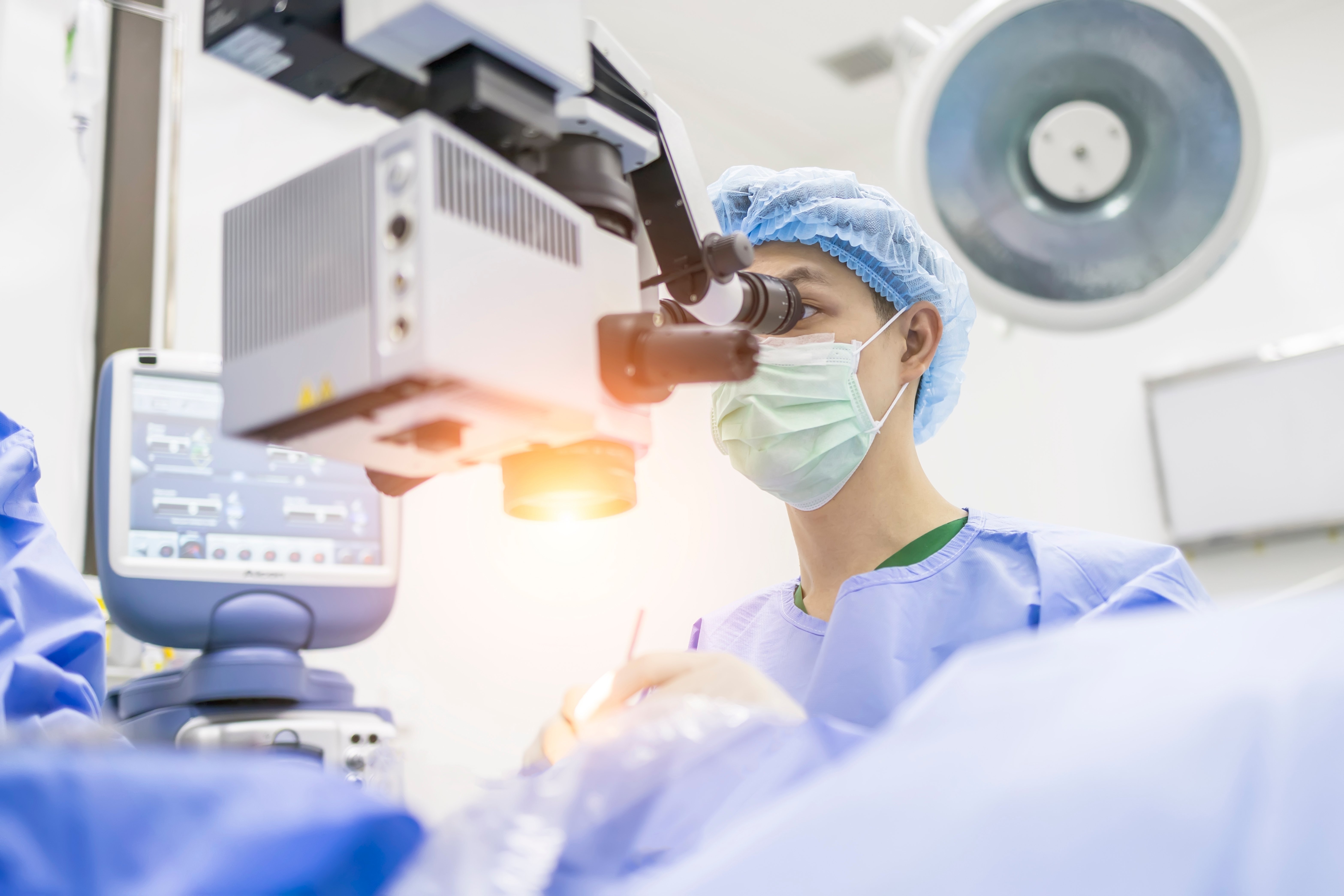
Case Study
Medical device company enhances supply chain control by integrating Loftware with SAP
Download the case study to learn how this medical device company enhanced supply chain control by integrating...